

GUBING WANG
HELLO I'M GUBING
I LOVE SOLVING PROBLEMS
Sport Innovation Challenge

Problem breifing
How to cycle more efficiently has always been a problem for cyclists, and especially for Paralympics cyclists who tend to receive less feedback from and less control over the bike. This project aimed to design an instrumented bike together with its software system that can measure the applied forces on the bike, and thus providing feedback for improvement in the cycling gait of Paralympics cyclists, and potentially for all the cyclists.
My task:
-
Determined the positions to place strain gauges from solid mechanics knowledge and literature research. (Identified the weight distribution can be more effectively measured by locating strain gauges at the front forks and chain stays than at the seat and proposed it in the group meeting, it is later figured out that strain gauges at the front forks solely is adequate for measuring weight distribution.)
-
Involved with interviewing Jon-Allen Butterworth.
-
Presented our project as a group.
-
Contributed to the group report.
-
Demonstrated our project to the public at Imperial Festival 2014.
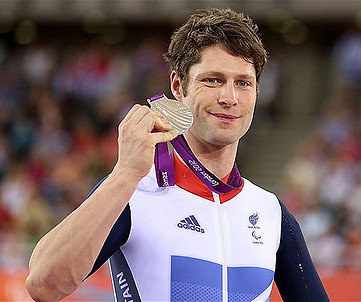
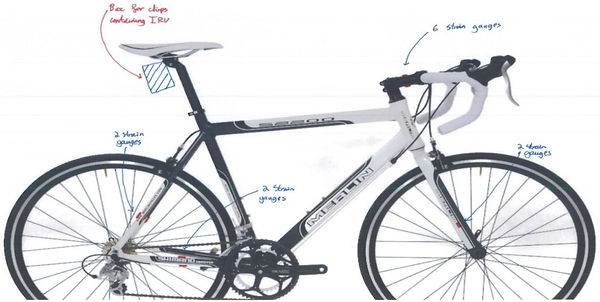
Interviews and insights
We decided to focus our design on Paralympics cyclist with one particular physical disability. Jon-Allen Butterworth is a British Paralympics cyclist and lost his left arm so he cannot sense how much force is being used to control the handlebars of the bike with the prosthetic arm. During the interview, he also showed interests in knowing his weight distribution and how much he swings side to side during cycling. Surprisingly he thinks viewing the feedback in real-time is distracting and prefers to view the data after the training. He would like to zoom into a particular time frame when analysing the data.
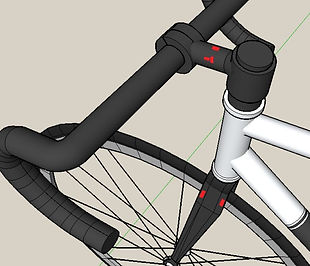
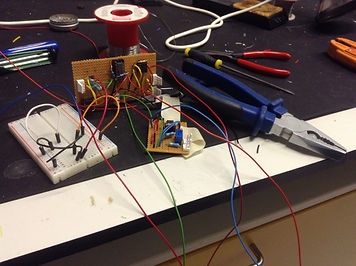
Ideas exploration

We have explored the sensors that we could use to measure these parameters, where to apply these sensors and how to attach them. We investigated different data processors in terms of the number of their input terminals, cost, size and electricity consumption.

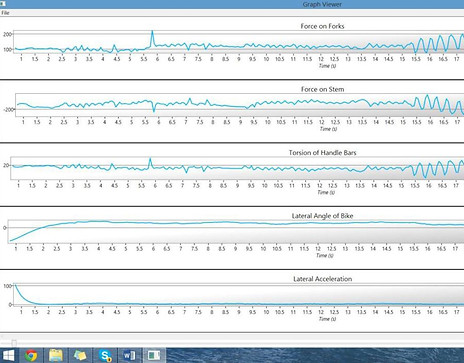
Final design
The final design contains strain gauges, Wheatstone bridge circuits, amplification circuits, an Arduino, an accelerometer, a gyroscope, batteries, a MicroSD card, a seat bag and a GUI (Graphical User Interface).
Strain gauges were attached around the stem and fork blades of a bicycle. Via Wheatstone bridge and amplification circuits, the strains applied to the bike were translated into voltage values that were read into the Arduino. Subsequently, the forces applied at the locations where strains were detected were deduced, and the data was stored on the MicroSD card together with speed and tilt data collected by the accelerometer and the gyroscope respectively. The whole circuits is powered by batteries and stored in the seat bag so that they can be easily removed before competition. The information could be displayed by the GUI and analyzed by a coach/ athlete after the event to improve cycling form and maximize effectiveness. The end product was not calibrated but was able to display the relative magnitude of forces applied to the bike over a recording period.​
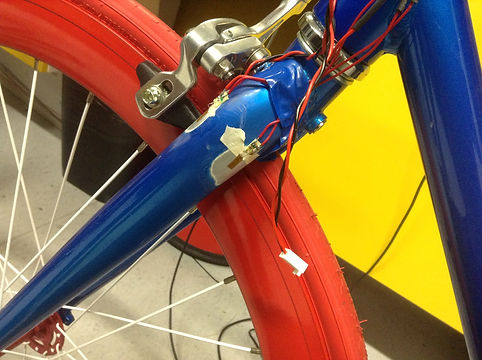

Prototyping
The strain gauges were attached to the bike according to the Vishay guidelines, the circuits are constructed on breadboards, and the accelerometer and the gyroscope are taped on the bike frame. The aesthetics of the prototype can be improved by printing all the circuitry on a Printed Circuit Board (PCB) and designing a plastic housing for the electronics. Our project was selected to be displayed on Imperial Festival 2014.

